Metal mesh stamped with precision perforations.
The Art of Precision A Look into a Stamping Perforated Metal Mesh Factory
In the heart of industrial advancement, stamping perforated metal mesh factories stand as testaments to the precision and innovation that drive modern manufacturing. These facilities specialize in the production of high-quality, perforated metal sheets, which have an array of applications ranging from architectural design to industrial filtration.
The process begins with large rolls of metal, typically stainless steel, aluminum, or other alloys, selected for their durability and resistance to corrosion. The first step is the stamping operation, where powerful presses equipped with specially designed dies punch out patterns with incredible accuracy. Each strike creates a perfectly formed hole, contributing to the overall aesthetic and functional requirements of the mesh.
The machinery in these factories is state-of-the-art, capable of micro-adjustments to ensure every sheet meets exacting standards. Technicians monitor each phase closely, adjusting for factors such as metal thickness, hole diameter, and pattern spacing. This meticulous approach ensures that the final product can be used in critical environments such as in food processing, where hygiene is paramount, or in construction, where it might serve as part of a load-bearing façade.
Quality control is stringent throughout the manufacturing process. Inspectors use advanced measuring tools to verify the consistency of the holes and the flatness of the sheets Inspectors use advanced measuring tools to verify the consistency of the holes and the flatness of the sheets
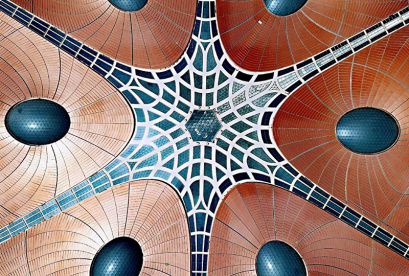
Inspectors use advanced measuring tools to verify the consistency of the holes and the flatness of the sheets Inspectors use advanced measuring tools to verify the consistency of the holes and the flatness of the sheets
stamping perforated metal mesh factory. Any deviation from the specified parameters results in immediate corrective action to maintain product integrity.
Sustainability is also a key focus in these factories. Efforts are made to recycle scrap metal and minimize waste during production. Furthermore, the efficiency of these operations is continually improved to reduce energy consumption without sacrificing output quality.
The finished perforated metal sheets leave the factory in various sizes, ready to be cut, shaped, and integrated into their designated projects. From simple ventilation needs to complex architectural designs, the versatility of these products is matched only by the expertise found within the walls of a stamping perforated metal mesh factory. Here, amidst the hum of machinery and the sharp ring of metal being shaped, the future of construction and industry is being crafted with precision, innovation, and an unwavering commitment to quality.