Welding perforated sheet metal fabrication.
The Evolution of Welding Perforated Sheet Factories
The advent of welding technology has revolutionized various industries, and the production of perforated sheets is no exception. Welding perforated sheet factories specialize in the creation of metal sheets with tiny holes, which serve a multitude of purposes ranging from filtration to decorative uses. These factories have evolved significantly over time, incorporating advanced technologies and techniques to meet the ever-increasing demand for precision and quality in perforated sheet manufacturing.
In the early days, the process of creating perforated sheets was labor-intensive and time-consuming. It involved manually punching holes into the metal using simple tools. However, with the introduction of welding technology, the process became more efficient and precise. Modern welding perforated sheet factories utilize automated machines that can quickly and accurately punch thousands of holes into a sheet of metal. This not only improves productivity but also ensures consistency in hole size and placement.
One key aspect of welding perforated sheet factories is their ability to handle different materials. They often work with various types of metals, including stainless steel, aluminum, and copper. Each material requires specific welding techniques and parameters to ensure optimal results Each material requires specific welding techniques and parameters to ensure optimal results
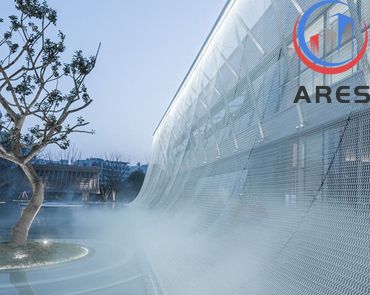
Each material requires specific welding techniques and parameters to ensure optimal results Each material requires specific welding techniques and parameters to ensure optimal results
welding perforated sheet factories. For instance, stainless steel needs a higher heat input during welding compared to aluminum to prevent cracking or warping. By understanding these nuances, welding perforated sheet factories can cater to diverse applications while maintaining high standards of quality.
Moreover, these factories pay close attention to the finishing processes after welding. They may employ techniques such as sandblasting or electropolishing to enhance the appearance and durability of the perforated sheets. Sandblasting removes any surface impurities or irregularities, giving the sheet a smooth finish. On the other hand, electropolishing involves an electrochemical process that refines the surface by dissolving microscopic rough spots, resulting in a shiny and reflective surface.
In conclusion, welding perforated sheet factories have come a long way since their inception. Through the adoption of advanced technologies and techniques, they have been able to streamline their production processes, expand their material capabilities, and improve overall product quality. As we continue to discover new applications for perforated sheets, it is likely that these factories will further innovate and adapt to meet future demands.