In the expansive world of construction and industrial manufacturing, perforated metal sheet factories stand as pivotal pillars, seamlessly blending innovative technology with precise engineering. These factories are crucial in manufacturing perforated metal sheets, which have a plethora of applications across various sectors, ranging from architecture to automotive industries. Understanding the intricacies within these factories unveils a fascinating convergence of expertise, authority, and trustworthiness, ensuring the consistent quality that global markets depend on.
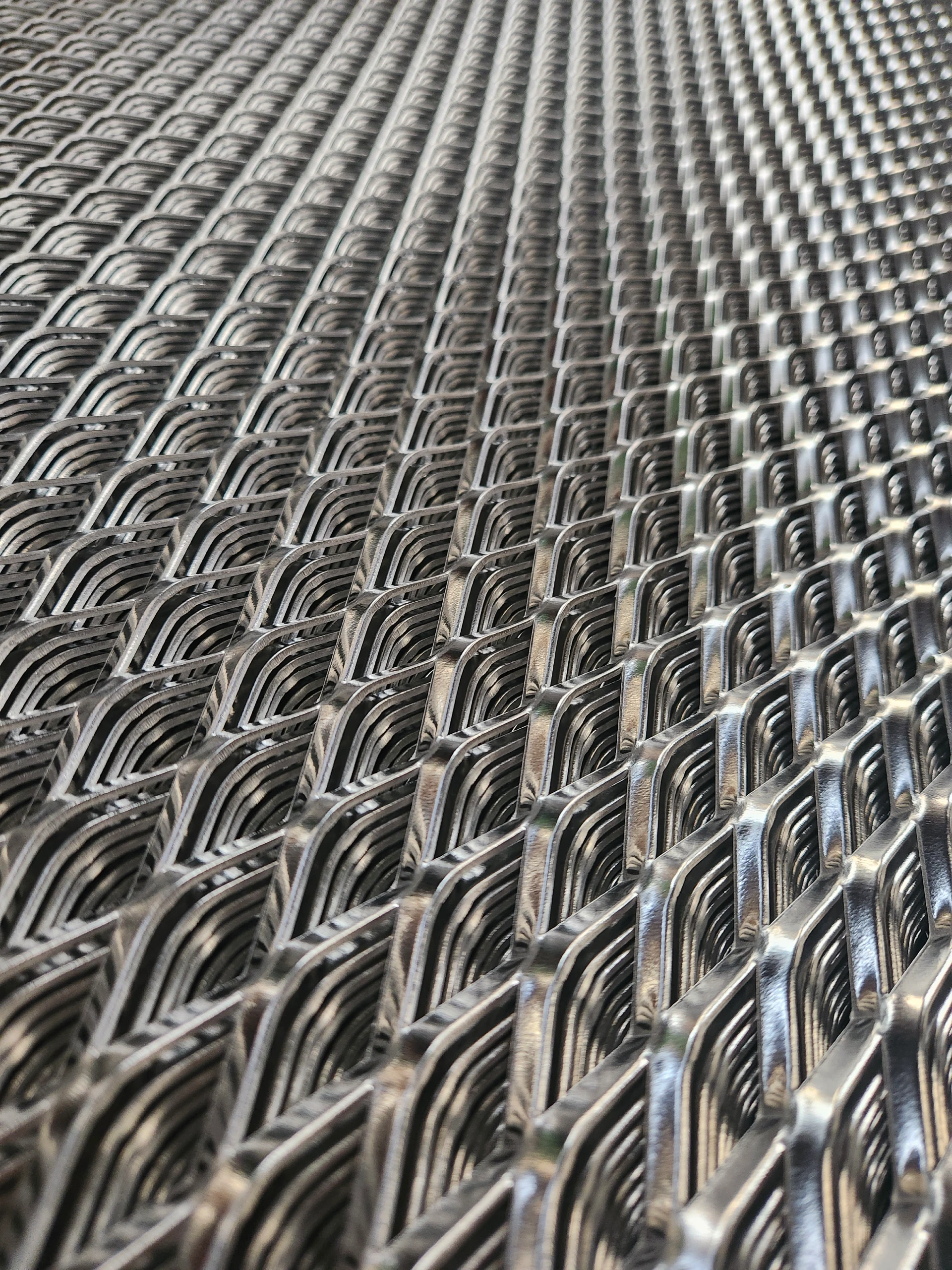
Perforated metal sheets are quintessential for a myriad of applications due to their versatility, durability, and aesthetic appeal. A comprehensive exploration into a perforated metal sheet factory reveals a well-oiled machine of precision engineering and skilled craftsmanship. At the heart of these operations lies a commitment to producing high-quality, reliable sheets that meet the specific needs of diverse industries.
The manufacturing process begins with selecting the finest raw materials, primarily high-grade metals such as stainless steel, aluminum, and brass. This selection process showcases the factory's expertise in ensuring that only materials that provide the required strength, corrosion resistance, and longevity are utilized. The choice of metal significantly impacts the performance and durability of the final product, influencing the factory's authority in the industry due to their meticulous material selection protocols.
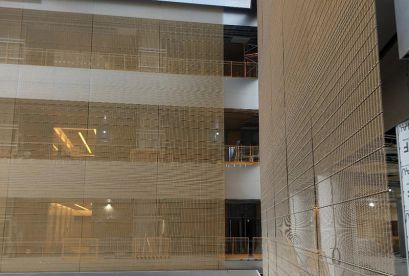
Once raw materials are selected, the perforation process commences. This involves utilizing state-of-the-art CNC machinery and advanced software to achieve precise hole patterns and configurations. This technological integration not only enhances efficiency but also ensures that each perforated sheet aligns with international quality standards. The machinery employed in these factories is continually updated, reflecting the factory's commitment to utilizing cutting-edge technology to maintain its competitive edge.
Expertise within a perforated metal sheet factory is further demonstrated through the customization services offered. Factories readily adapt to burgeoning market demands by providing bespoke perforation solutions tailored to individual client specifications. This adaptability is indicative of a profound understanding of the nuances involved in different industry requirements, be it for acoustic control panels, filters, or decorative facades. The capacity to customize reflects the factory's authoritative position in the market, leveraging both technical know-how and innovative design strategies.
perforated metal sheet factory
Quality control is a cornerstone in these manufacturing settings. Stringent quality checks are meticulously implemented at various production stages to ensure that every perforated sheet meets rigorous standards. This not only involves dimensional checks and material composition analysis but also real-world performance testing to validate durability and functional effectiveness. Such stringent quality assurance protocols enhance trustworthiness, reassuring clients of the product’s reliability and consistency in performance.
Experts in the field understand the environmental implications of metal manufacturing, and as such, modern perforated metal sheet factories often incorporate sustainable practices. Advanced recycling methods, waste minimization tactics, and energy-efficient production processes underpin their operations. This proactive approach towards sustainability highlights the factory's responsibility not only to their clients but also to the environment, aligning with global standards for sustainable manufacturing practices.
Communication and customer service form the backbone of maintaining trust and authority in the industry. Perforated metal sheet factories prioritize transparent communication, offering technical support and guidance throughout the client’s decision-making process. A team of skilled professionals is readily available to assist in design considerations and to offer insights into the material and pattern selection that best suits the client's requirements.
The success and reputation of a perforated metal sheet factory are, therefore, rooted in its unwavering commitment to quality, innovation, and customer satisfaction. By continually pushing the boundaries of what is possible with perforated technology, these factories not only satisfy current market demands but also set new standards for excellence. Through a blend of experience, expertise, authoritativeness, and trustworthiness, they anchor themselves as integral contributors to advancements within the construction and manufacturing landscapes, ensuring they remain indispensable assets in an ever-evolving global market.