aluminium Perforated Sheet Manufacturing A Comprehensive Overview
Aluminium perforated sheets, an innovative and versatile material, have found their way into a myriad of industries due to their unique blend of strength, lightweight, and aesthetic appeal. The manufacturing process of these sheets in factories is a testament to the fusion of modern technology and precision engineering.
A dedicated aluminium perforated sheet factory is a hub of advanced machinery and skilled craftsmanship. The journey from raw aluminium ingots to finished perforated sheets begins with the selection of high-quality aluminium alloys. These alloys, chosen for their specific properties, can range from pure aluminium to those blended with other elements to enhance durability, corrosion resistance, or formability.
The first step in the manufacturing process is melting. The aluminium ingots are heated to extreme temperatures in a furnace until they liquefy. This molten aluminium is then poured into a casting machine where it cools and solidifies into flat slabs, also known as billets. These billets are subsequently rolled into thin sheets using a series of rollers, ensuring uniform thickness and a smooth surface finish.
The next critical stage is perforation. Here, the aluminium sheets pass through a high-tech perforating machine equipped with precisely designed dies. The machine punches holes of various shapes and sizes into the sheet according to the client's specifications. The perforation pattern can be customized to meet architectural, acoustic, or filtration requirements, ranging from simple round holes to complex geometric designs The perforation pattern can be customized to meet architectural, acoustic, or filtration requirements, ranging from simple round holes to complex geometric designs
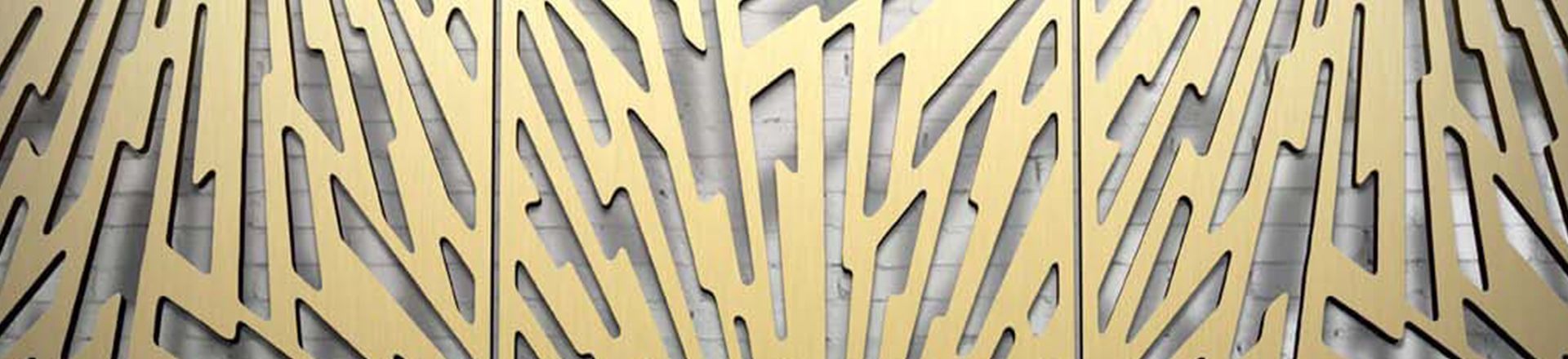
The perforation pattern can be customized to meet architectural, acoustic, or filtration requirements, ranging from simple round holes to complex geometric designs The perforation pattern can be customized to meet architectural, acoustic, or filtration requirements, ranging from simple round holes to complex geometric designs
aluminium perforated sheet factory.
Quality control is paramount throughout the process. Factory technicians regularly inspect the sheets for dimensional accuracy, hole consistency, and any defects. Advanced computer-aided systems aid in this process, ensuring each sheet meets stringent quality standards.
Once the perforation is complete, the sheets undergo secondary operations like cutting, bending, or edge finishing, depending on the end-use application. For instance, if the sheet is intended for architectural use, it might be powder-coated or anodized to add color or improve weather resistance.
In a typical aluminium perforated sheet factory, sustainability is also a key consideration. Scrap metal is recycled, reducing waste and environmental impact. Furthermore, aluminium itself is 100% recyclable, making it an eco-friendly choice.
In conclusion, aluminium perforated sheet manufacturing is a blend of art and science, requiring precise engineering and a deep understanding of material properties. These factories, with their state-of-the-art technology and commitment to quality, play a crucial role in delivering customised solutions that cater to diverse industrial and design needs. Whether it's for architectural facades, sound barriers, or filtration systems, aluminium perforated sheets continue to shape our built environment, showcasing the versatility and resilience of this remarkable material.