Laser Cutting Perforated Metal Factories
Laser Cutting and Perforated Metal Factories Revolutionizing Manufacturing
In the realm of manufacturing, laser cutting technology has emerged as a game-changer. This advanced technique allows for precise and intricate cuts in a variety of materials, including metals. The integration of laser cutting into perforated metal factories has revolutionized the production process, enabling manufacturers to produce high-quality products with increased efficiency and reduced costs.
Perforated metal, a versatile material commonly used in a wide range of applications, such as filtration systems, soundproofing, and architectural design, benefits greatly from laser cutting technology. Traditional methods of cutting perforated metal, such as punching or shearing, often result in rough edges and limitations in terms of precision and complexity. In contrast, laser cutting offers unparalleled accuracy, allowing for holes of any size and shape to be created with remarkable detail.
The advantages of laser cutting in perforated metal factories are manifold. Firstly, it significantly improves the quality of the final product. The clean and precise cuts produced by lasers eliminate the need for secondary finishing, reducing waste and improving overall product quality. Secondly, laser cutting is faster than traditional methods, resulting in increased productivity and reduced lead times Secondly, laser cutting is faster than traditional methods, resulting in increased productivity and reduced lead times
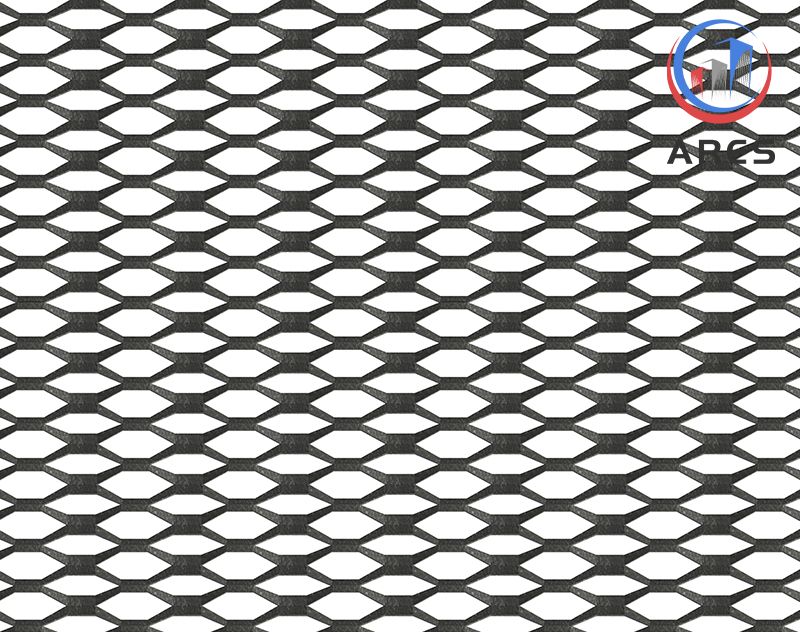
Secondly, laser cutting is faster than traditional methods, resulting in increased productivity and reduced lead times Secondly, laser cutting is faster than traditional methods, resulting in increased productivity and reduced lead times
laser cut perforated metal factories. This is particularly beneficial in industries where time is of the essence, such as automotive or aerospace.
Furthermore, laser cutting is highly adaptable and can be used to cut a wide range of metal types, including stainless steel, aluminum, and copper. This versatility allows manufacturers to produce custom perforated metal products tailored to their specific needs. Additionally, the use of lasers in the manufacturing process reduces the risk of human error, as the machine operates with precision and consistency.
In conclusion, the integration of laser cutting technology into perforated metal factories has brought about significant advancements in the manufacturing industry. The ability to produce high-quality, custom perforated metal products with increased efficiency and reduced costs has made laser cutting an indispensable tool for manufacturers worldwide. As this technology continues to evolve, we can expect to see even more innovative applications and improvements in the field of manufacturing.