Metal Sheet Perforation Services Cutting and Customization Factory
Cutting Perforated Metal Sheet Factory A Modern Manufacturing Marvel
In the heart of industrial progress lies a specialized domain where precision meets innovation the cutting perforated metal sheet factory. This manufacturing marvel is not just a facility but a beacon of modern technology, showcasing the epitome of craftsmanship and engineering excellence.
As you step into one of these state-of-the-art factories, the symphony of machines immediately captures your attention. The rhythmic hum of cutting devices and the punctual clinking of punch presses create an atmosphere that buzzes with productivity. Here, rolls of pristine metal sheets enter the production line, destined to be transformed into intricately perforated masterpieces.
The process begins with meticulous planning, where computer-aided design (CAD) software aids engineers in crafting blueprints for each unique perforation pattern. These designs are then transferred to the cutting machinery, which could range from laser cutters to punch presses, depending on the complexity and size of the project at hand.
Laser cutters, wielding precise beams of light, can etch even the most delicate patterns into the metal's surface with surgical accuracy. They are favored for their ability to make clean, smooth cuts without the physical strain of traditional cutting methods. In contrast, punch presses use physical force to stamp out patterns, often employed when robustness and speed are required over intricate detailing In contrast, punch presses use physical force to stamp out patterns, often employed when robustness and speed are required over intricate detailing
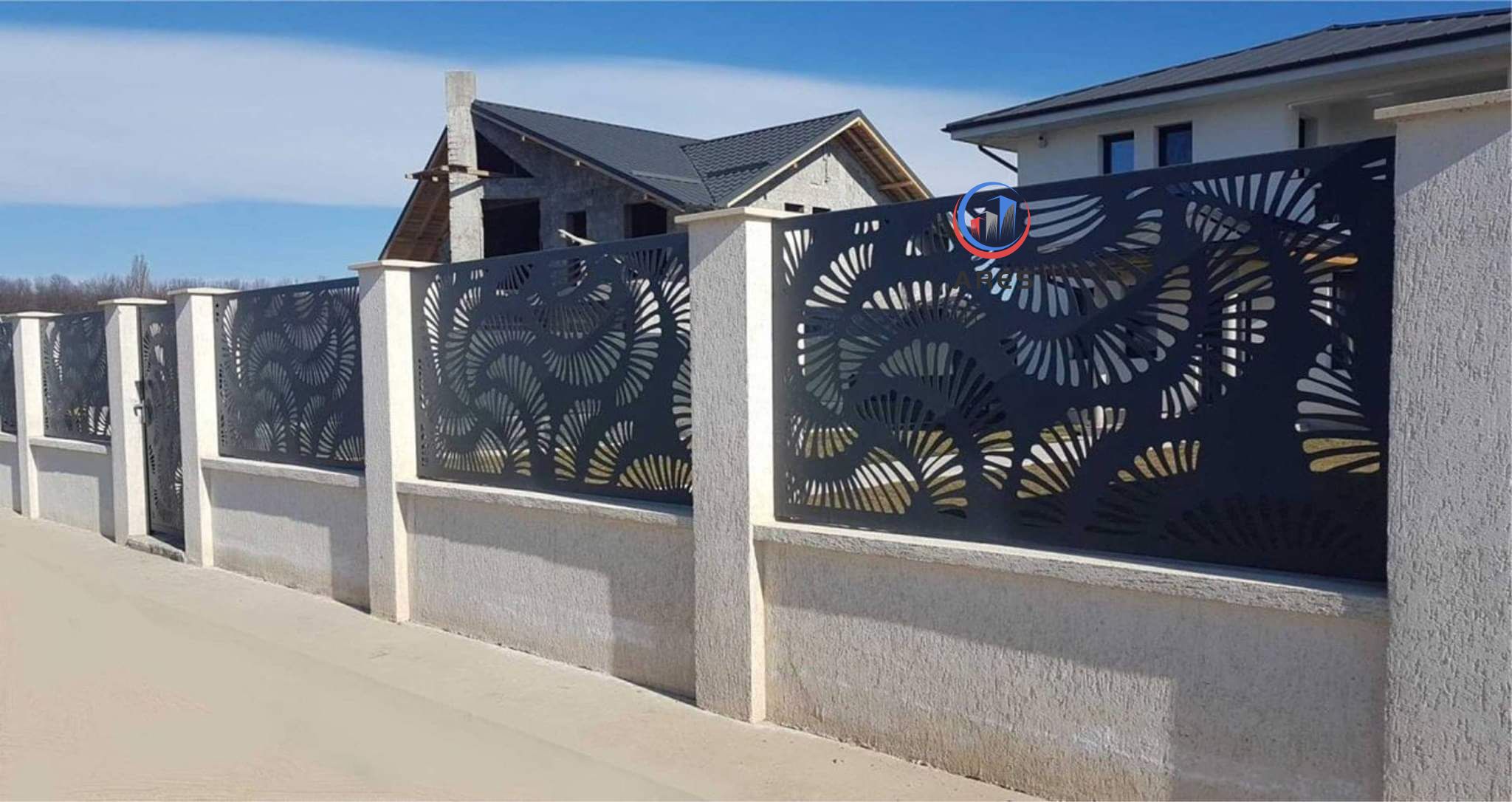
In contrast, punch presses use physical force to stamp out patterns, often employed when robustness and speed are required over intricate detailing In contrast, punch presses use physical force to stamp out patterns, often employed when robustness and speed are required over intricate detailing
cutting perforated metal sheet factory.
Quality control is paramount in such facilities. Technicians regularly inspect the perforated sheets at various stages to ensure that each hole is precisely where it should be, adhering to strict tolerances. Any deviation could compromise the structural integrity of the final product or alter its aesthetic appeal.
The end products of these factories are as diverse as they are essential. From filtration systems that require precise airflow to architectural elements that demand visual elegance, the applications of perforated metal sheets are limitless. They find their way into automotive parts, soundproofing materials, decorative facades, and countless other industries where form meets function.
In conclusion, the cutting perforated metal sheet factory stands as a testament to human innovation and the relentless pursuit of perfection. It is a place where raw materials undergo a transformation both artistic and utilitarian, serving as a critical backbone to numerous sectors that drive our modern world forward.