Perforated metal sheet mesh stands as a testament to engineering ingenuity, uniting aesthetics with utilitarian function. These precision-engineered materials have carved a significant niche across various industries, transforming how professionals approach structural and design challenges. Understanding the multifaceted applications and benefits of perforated metal sheet mesh is crucial for professionals seeking durable and effective solutions.

Perforated metal sheet mesh is created through the meticulous process of punching holes into metal sheets, forming intricate patterns that enhance both function and style. This product is manufactured using an array of metals such as stainless steel, aluminum, copper, and brass, each offering distinct characteristics tailored to specific applications. Through expert manipulation of materials, manufacturers can customize hole size, pattern, and sheet thickness to meet precise specifications, thus demonstrating the product’s versatility.
In the architecture and construction sectors, perforated metal sheet mesh plays an indispensable role. Architects and builders are increasingly embracing its use in designing facades and curtain walls. Not only does it provide an aesthetically pleasing screen, but it also offers essential benefits such as improved ventilation, solar shading, and acoustic control. These properties make it a prime choice for those looking to enhance building efficiency while maintaining a modern aesthetic. The eco-friendly nature of these materials further boosts their appeal, aligning with the growing demand for sustainable building solutions.
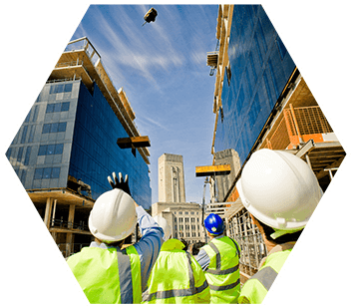
The automotive industry also harnesses the power of perforated metal sheet mesh. This material is a staple in manufacturing automotive components due to its lightweight yet robust characteristics. It is commonly used in fabricating grilles, filters, and radiator covers, owing to its ability to withstand harsh environmental conditions while providing necessary ventilation and protection. Its application extends to sound absorption, reducing noise generated by engines and road vibrations, thus contributing to a quieter and more comfortable driving experience.
Perforated metal sheet mesh’s utility extends to industrial applications as well. In sectors such as agriculture and mining, these meshes serve as effective sieves and separators. Their ability to handle heavy loads and resist wear under strenuous conditions makes them an invaluable tool in processes like sorting, screening, and filtering. The precise perforation patterns can be customized to control the passage of particles, ensuring efficiency and accuracy in operations.
perforated metal sheet mesh
In addition to its practical applications, perforated metal sheet mesh is celebrated for its decorative potential. Interior designers utilize it to create unique wall panels, ceilings, and partition systems, adding a contemporary flair to spaces. The adaptability of these meshes supports innovation, allowing designers to experiment with patterns and lighting effects that transform an ordinary space into an intriguing visual experience.
The choice of perforated metal sheet mesh not only enhances design and functionality but also outperforms alternative materials in terms of longevity and maintenance. The durability of metal, coupled with its resistance to corrosion and environmental damage, offers a long-lasting solution with minimal upkeep. This reliability builds trust with clients, as investments in these materials promise reduced long-term costs and enhanced performance.
Each project utilizing perforated metal sheet mesh benefits from the depth of expertise manufacturers and suppliers bring. Professionals engage in rigorous quality assessments, ensuring each sheet meets stringent standards before it reaches the client. This commitment to excellence reaffirms the product’s credibility, securing its position as a preferred choice for those who require dependable and customizable solutions.
Perforated metal sheet mesh epitomizes the balance between functionality and design. With its wide-ranging applications and benefits, it remains an indispensable material across industries seeking efficiency, sustainability, and innovation. The continuous advancement in manufacturing technology promises further evolution in the capabilities and applications of these versatile materials, ensuring they remain at the forefront of industrial and architectural solutions.