solidworks perforated sheet
Designing with perforated sheets in SOLIDWORKS offers a variety of opportunities, notably for engineers and manufacturers aiming to innovate across sectors such as aerospace, automotive, and industrial design. Utilizing a robust platform like SOLIDWORKS can enhance your creative output and streamline your design process. Here, we explore the intricacies and advantages of working with perforated sheets within this powerful CAD environment.
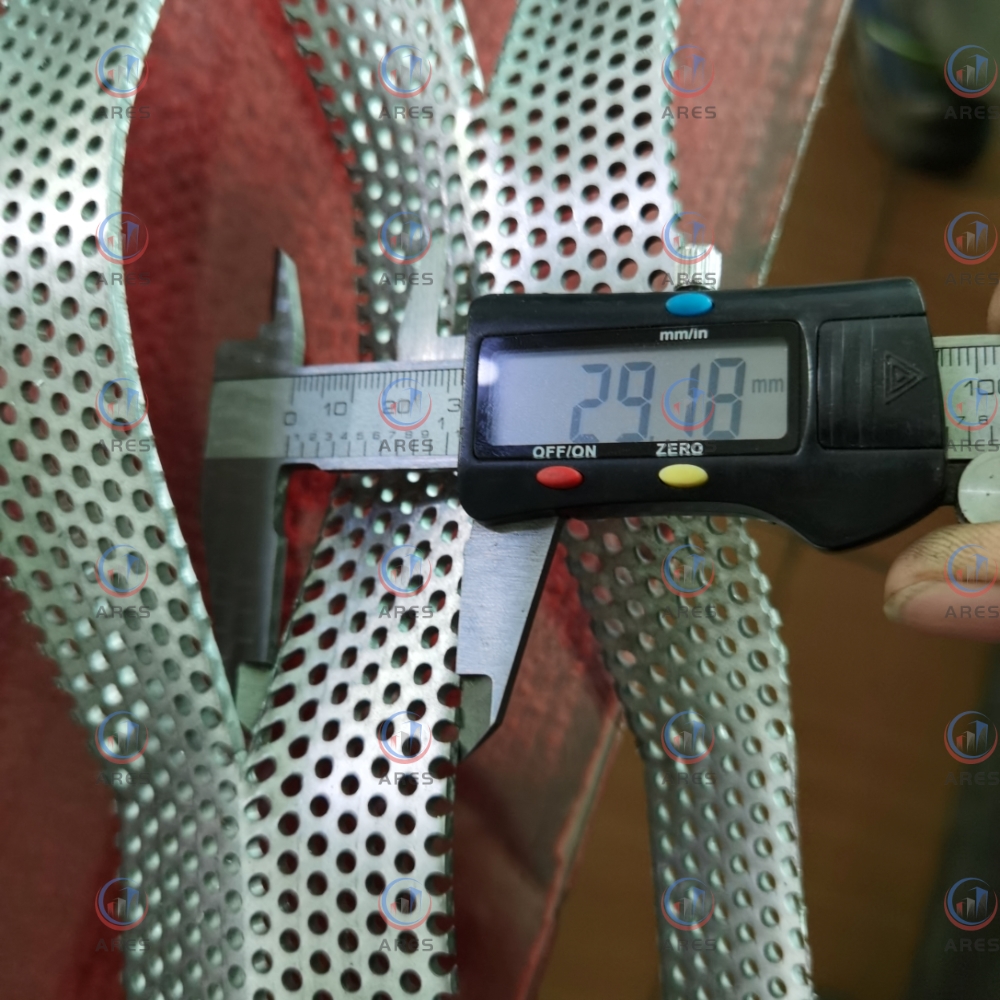
At its core,
the allure of perforated sheets lies in their versatility. They are not only crucial for aesthetic appeal in design but also serve functional purposes like ventilation, filtration, and noise reduction. Designing these complex patterns manually could be daunting, but SOLIDWORKS simplifies the process, offering tools that blend expertise with ease of use. Drawing from years of experience in CAD design, users can leverage these features to transform basic designs into functional products.
To begin, the FeatureManager design tree in SOLIDWORKS provides an intuitive interface for creating perforated patterns. Importantly, users can access an extensive library of pattern templates or customize their unique designs. This flexibility is essential for tailoring projects to specific requirements, whether they involve architectural elements or intricate industrial components.
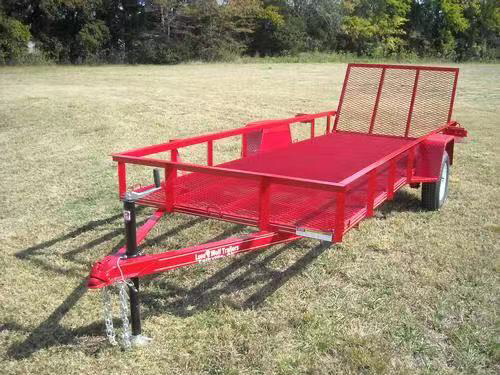
Professional application of perforated sheets requires a deep understanding of material properties and stress factors. SOLIDWORKS excels here, offering simulation tools that predict how designs will perform under various real-world conditions. These simulations are crucial for ensuring structural integrity and can prevent costly errors or product failures. When designing with perforated sheets, utilizing SOLIDWORKS' Finite Element Analysis (FEA) can help identify potential stress points and optimize the distribution of holes to maintain strength while achieving desired functionality.
solidworks perforated sheet
For companies keen to maintain an edge in product development, expertise in leveraging SOLIDWORKS’ parametric design capabilities is invaluable. The tool’s parametric features allow for quick adjustments in design dimensions, which is a boon for iterative testing and rapid prototyping phases. By accommodating these changes seamlessly, SOLIDWORKS not only enhances productivity but also ensures continuity in design improvements and scalability.
Another vital aspect of working with perforated sheets in SOLIDWORKS is the integration with sheet metal functionality. Expertise in this area is indispensable, especially given that many perforated sheet applications involve metal. SOLIDWORKS Sheet Metal tools enable detailed unfolding of designs to ensure precision in cutting and bending operations. Utilizing these features can significantly reduce manufacturing lead times and resource expenditure.
Credibility in manufacturing and design also hinges on the authority granted by adhering to industry standards. SOLIDWORKS supports adherence to various standards by enabling precise documentation and drawing generation, which are essential for communicating design intent clearly to stakeholders and partners involved in the manufacturing process. This capability fosters trust and accountability in collaborative environments, where precise communication is paramount.
In conclusion, the journey of designing perforated sheets in SOLIDWORKS is enriched by the software’s comprehensive suite of tools that enhance functionality, efficiency, and reliability. Whether you're an engineer focused on innovative solutions or a company striving for competitive superiority, integrating these insights into your design process can unlock endless possibilities in product development and establish a leadership position in your field.